Optimization of Sulfur and Phosphorus Content in Gray Iron Brake Discs
In the application of gray iron materials, especially for high-grade gray iron components like brake discs, excessively low sulfur (S) and phosphorus (P) content is not ideal. Instead, maintaining appropriate levels of these elements is critical to ensuring optimal performance and quality.
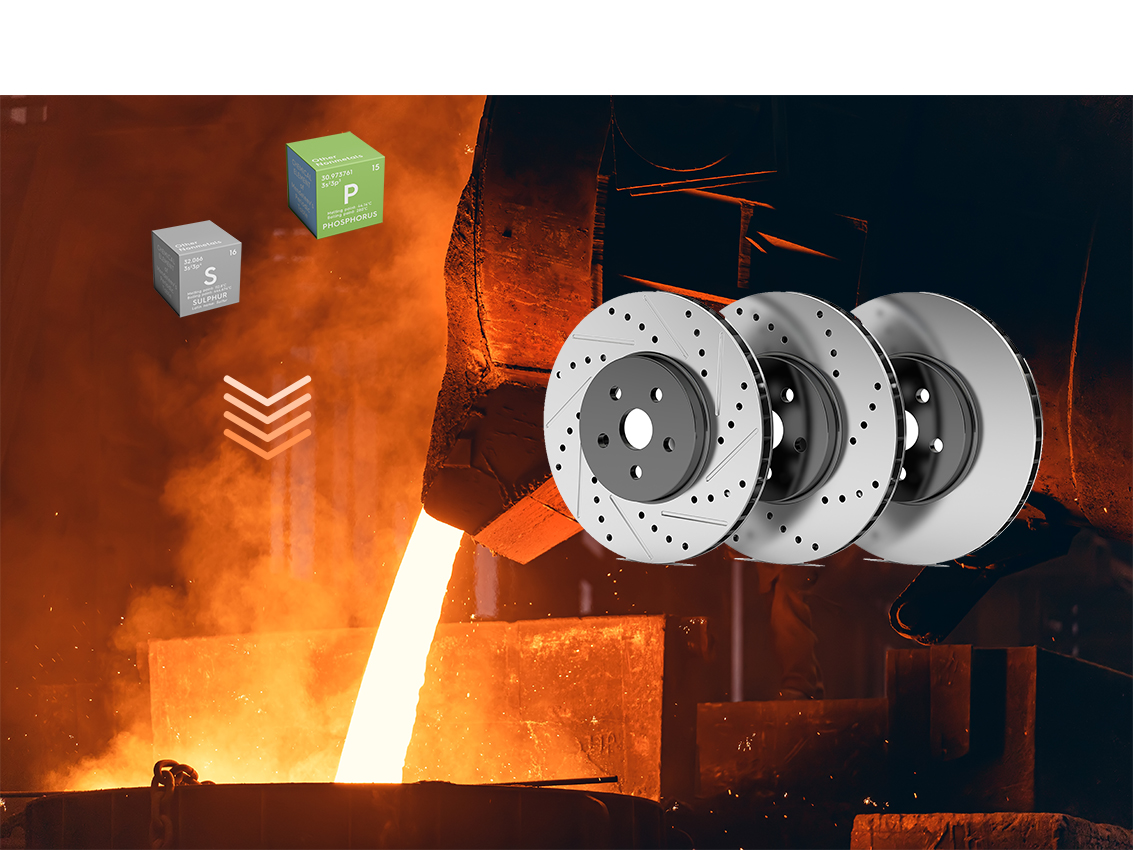
During the casting of gray iron brake discs, sulfides serve as nucleation sites for eutectic graphite while inhibiting the excessive growth of eutectic colonies. However, sulfur also promotes the formation of brittle white iron structures. Therefore, a balanced sulfur content is essential for improving brake disc quality.
White Iron Control: A sulfur content of 0.041% minimizes white iron layer thickness, regardless of inoculation. At this level, eutectic colony density remains moderate, balancing graphite distribution and structural integrity.
Experimental data reveals:
Hardness Response: For both inoculated and non-inoculated brake discs, Brinell hardness increases rapidly when S ≤ 0.04% (slope ≈ 12 HB/%S) and stabilizes beyond S > 0.04%.
Microstructure Transformation: At S = 0.006%, the matrix contains 40% pearlite; at S = 0.04%, pearlite reaches 100%.
Strength Optimization: Tensile strength peaks (≥250 MPa) at S = 0.04–0.06%, coinciding with the lowest relative hardness.
Inoculation Efficiency: Sulfur below 0.04% impairs the effectiveness of Sr-SiFe inoculants, compromising microstructure refinement.
While phosphorus forms low-melting-point (80–120°C lower than the matrix) binary/ternary phosphide eutectics, which may cause shrinkage and cold cracks, controlled phosphorus levels offer benefits:
Anti-Sand Adhesion:
P = 0.02–0.04%: Severe sand adhesion occurs, increasing cleaning time by 35%.
P = 0.09–0.12%: Sand adhesion is eliminated, reducing iron penetration depth by 40%.
Mechanism: Phosphorus decreases molten iron infiltration during solidification, particularly at thermal joints (e.g., internal cavities), where graphite expansion-driven sand adhesion occurs.
Wear Resistance: P-Cu-Ti alloyed cast iron (P = 0.35–0.65%) forms wear-resistant phosphide eutectic networks, reducing friction coefficients by 18%.
Flowability: Phosphorus improves iron fluidity by 25%, critical for thin-walled brake disc designs.
Surface Finish: P = 0.3–0.5% ensures sharp casting edges and smooth surfaces, analogous to applications like sewing machine parts (P = 0.3%) and radiators (P = 0.4–0.5%).
Sulfur Control: Use ferro-sulfur for precise adjustments and rare-earth treatments to mitigate sulfur embrittlement.
Phosphorus Management: Regulate via recycled material ratios and targeted ferro-phosphorus additions.
Quality Monitoring:
This composition has been validated in automotive brake disc production, achieving 98.7% yield and meeting SAE J431 standards for hardness uniformity (±15 HB).
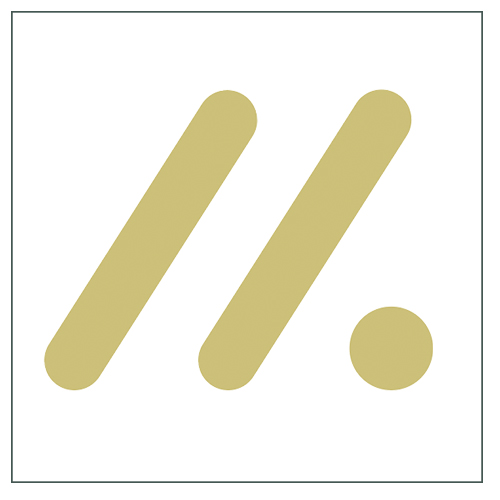
MIXHY, an ISO9001 certified firm. MIXHY now supply a wide range of car braking systems and components for cars, commercial vehicle, truck that covers brake disc, brake pad, brake caliper for the OE market, after-market.
Keywords: Gray iron brake discs, sulfur phosphorus optimization, eutectic colonies, white iron control, tensile strength, sand adhesion, wear resistance, casting composition.